American quick-service restaurant chain transforms operating model
American quick-service restaurant chain transforms operating model
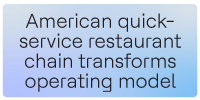
Customer Profile
A prominent American quick-service restaurant chain wanted to transform their business operating model, fast food manufacturing process and food quality assessment. The client’s existing business model was heavily dependent on manual interventions and traditional and legacy methodologies, which hindered the chain’s ability to harness emerging technologies to empower their 14,000-strong workforce. Consequently, they lacked scalability for expanding the business without compromising product quality.
Challenge
To meet ever-changing customer expectations, with rising commodity and labor costs, the client had to rapidly acquire new customers, while retaining existing ones. To deliver this, continuous product innovation, presentation consistency and agile delivery were needed. Achieving real-time visibility into their fast-food production cycle was also crucial to these goals.
- Migrating to an agile and scalable digital solution
- Addressing the company’s inadequacies with a
- forward-looking business model came with its
- share of challenges:
- Undue dependency on manual processes.
- Lack of objective-driven inclusion of new
- technologies.
- Absence of an organized business process
- and consistent customer journey
Solution
HCLTech’s expertise in modernizing legacy infrastructures, while making the most of existing components, made HCLTech the chain’s preferred partner with proven capability in implementing automation-driven agile delivery models and AI/ML-based analytics what the client was looking for. An end-to-end support was offered deploying a full-stack agile model encompassing all platforms, operations and data.
First, a thorough assessment of the client’s business and competitive environment and their technology landscape to determine the hardware and software used in food production and related operations was conducted. We then:
- Laid the foundation for the steps required to organize, re-skill, operate, measure and co-innovate to enhance production quality and efficiency.
- Introduced a fully automated, AI/ML-based quality grader system for product standardization across all outlets.
- Deployed agile methodology tools and processes to ensure product compliance.
- Mobilized data and platforms to monitor applications, product quality, operational efficiency and delivery timeliness.
- Implemented comparative cost and performance matrices, including:
- An insight-driven platform with built-in microservices.
- Automation-driven perpetual testing, integration and delivery pipelines.An automated regression test suite for online and POS-based purchases
Outcome
- Enhanced and consistent product quality using an automated grader that measures established quality characteristics of real-time product images via AI/ML algorithms.
- Precise traffic prediction and proactive stocking of inventory.
- Accurate understanding of customer expectations and enhanced customer retention through direct feedback.
- Recognition and incentivization of high-quality outlets.
- Delivering transformation at scale without service disruption, HCLTech enabled the client to achieve:
- The new operating model rewarded the company with a full menu of successes: reduced opex, greater control over food production and quality, enhanced efficiency and sustainable growth.
A German manufacturer of optical systems adopted Integrated Ophthalmology CARE Platform
A German manufacturer of optical systems adopted Integrated Ophthalmology CARE Platform
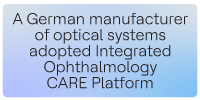
Challenges
- Reach product parity with competitor by providing a connected solution that would make transfer of data between the diagnostics and surgical instrument more efficient
- Single software platform to support on premise and cloud hosting. Cloud solution to be multi-tenant with full FDA Class III Compliance
- Manual Data transfer between diagnostics systems is time consuming and error prone
Solution
- Standardized and Integrated technology stack of CARE provided abstraction of complexity of cloud deployments and on-premise deployments
- Consulting lead requirement gathering to understand customer landscape
- Leverage CARE to build suitable software platform
- Reuse CARE modules with customisation for device care and monitoring
Outcome
- Reusable foundation of CARE reduced the development effort by 17%
- Pre-Tested components of CARE helped reduce QA efforts by 20%
- The connected device solution increase device usage; patient handling per day is increased up to 11%