Revolutionizing Customer Experience with HCLTech's Agile QSR Approach
A prominent American quick-service restaurant chain wanted to transform their business operating model, fast food manufacturing process and food quality assessment. The client’s existing business model was heavily dependent on manual interventions and traditional legacy methodologies, which hindered their ability to harness emerging technologies to empower their 14,000-strong workforce. Consequently, they lacked scalability for expanding the business without compromising on product quality.
The Challenge
Migrating to an agile and scalable digital solution
To meet ever-changing customer expectations, with rising commodity and labor costs, our client had to rapidly acquire new customers while retaining existing ones. Continuous product innovation, presentation consistency and agile delivery were needed to deliver this. Achieving real-time visibility into their fast-food production cycle was also crucial to these goals.
Addressing the company’s inadequacies with a forward-looking business model came with its share of challenges, including:
- Undue dependency on manual processes
- Lack of objective-driven inclusion of new technologies
- Absence of an organized business process and consistent customer journey
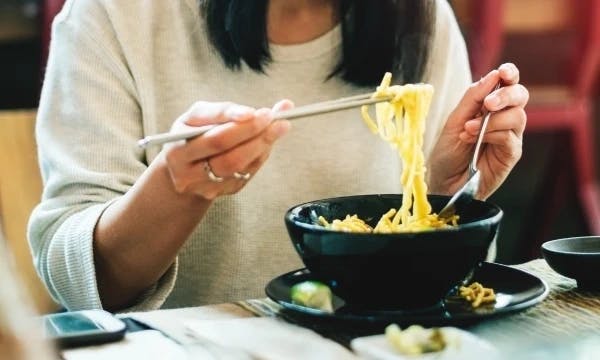
The Objective
Stable and sustainable sales growth
Like any other business, the chain’s fundamental objective was to increase sales in a stable, sustainable way. To accomplish this goal, their imperatives were to increase the variety of products, maintain high quality across all products and expedite the production line. They were ready to explore the untapped potential of cloud, analytics, AI/ML and IoT in achieving these business outcomes. They partnered with HCLTech to accelerate business growth via innovation, scalability, customer loyalty and stable growth.
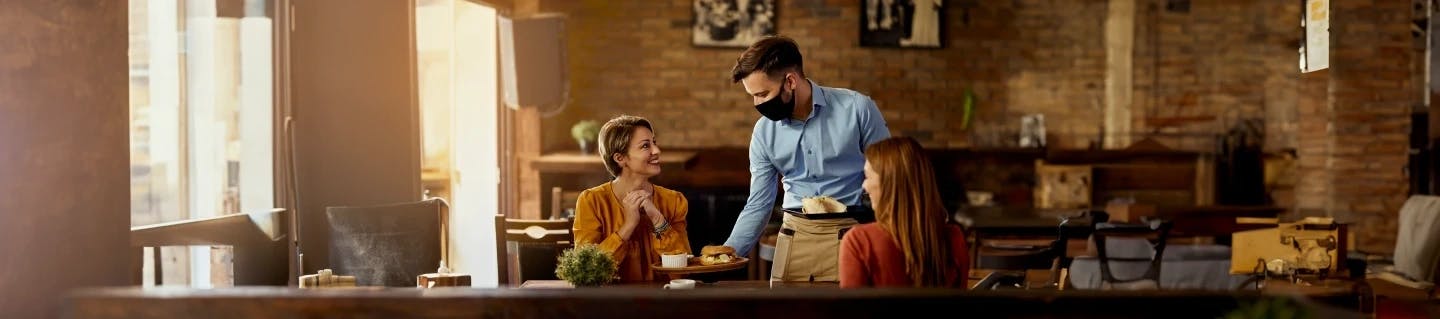
The Solution
Automation-driven agile delivery models and AI/ML-based analytics
HCLTech became the preferred partner for modernizing the chain's legacy infrastructure, utilizing our expertise in automation-driven agile delivery models and AI/ML-based analytics. End-to-end support was offered by deploying a full-stack agile model encompassing all platforms, operations and data. A thorough assessment was also conducted before laying the foundation for enhanced production quality and efficiency and introducing an AI/ML-based quality grader system for product standardization. HCLTech then:
- Laid the foundation for organizing, re-skilling, operating, measuring and co-innovating to enhance production quality and efficiency
- Introduced a fully automated, AI/ML-based quality grader system for product standardization across all outlets
- Deployed agile methodology tools and processes to ensure product compliance
- Mobilized data and platforms to monitor applications, product quality, operational efficiency and delivery timelines
- Implemented comparative cost and performance matrices, including:
- An insight-driven platform with built-in microservices
- Automation-driven perpetual testing, integration and delivery pipelines
- An automated regression test suite for online and POS-based purchases
The impact
A recipe for successful transformation at scale
Delivering transformation at scale without service disruption, HCLTech enabled oure client to achieve:
- Enhanced and consistent product quality using an automated grader that measures established quality characteristics of real-time product images via AI/ML algorithms
- Precise traffic prediction and proactive stocking of inventory
- Accurate understanding of customer expectations and enhanced customer retention through direct feedback
- Recognition and incentivization of high-quality outlets
The new operating model rewarded the company with a full menu of successes: reduced OpEx, greater control over food production and quality, enhanced efficiency and sustainable growth.