The Merriam-Webster Dictionary defines twinning as, “the act of producing or giving birth to twins.” In idustry, however, any digitized version of virtually anything physical is considered a Digital Twin (DT). Nonetheless, industry expectations of a DT also largely vary within the context of their business and operations. In this first of two blog posts, we explain how a DT impacts products and assets in a Smart Factory.
When Dr. Michael Grieves introduced the DT concept in 2002, it was a product-centric approach. With Product Lifecycle Management (PLM) as the process for handling product ideation through its actual realization and even disposal, a ‘cradle-to-grave’ (CTG) sort of analogy in the auto industry, most COTS solutions for DT focus on:
- Product design activity
- Product manufacturing process activities
- Product value creation
With the rise of IoT, however, wherein almost any physical part is capable of being made ‘smart,’ manufacturers and OEMs alike have felt the need to derive value from Smart Connected Assets in an industrial setup. The Smart Connected Asset DT is a subset of the Smart Connected Product DT but has unique needs that go beyond what the broader category requires [4]. These particular needs for Smart Connected Assets in an industrial setting cover several areas, such as [2]:
- Higher life of the asset or product: Translates to maintaining the evolutionary record that spans the entire asset life, as long as it is in service.
- Variability in configuration during service life: In certain industries, the actual configuration of an asset train must be part of the traceability and genealogy record of the products produced on that line. This means the twin must not only have a time-synchronized history but a product-linked history.
- Complexity of asset or product: Just as each asset is complex and unique, so too must the twin be unique and complex. However, the construction and maintenance of the twin must be automated and affordable.
- Service vs. replacement decisions: The life of most production assets spans a couple of decades, so the DT must incorporate adequate financial models to facilitate the simulation of alternative operations against forecasted repair costs.
- Community: Maintenance staff, operators, financial analysts, production engineers and process designers all form a community of users who need to interact with the twin. This means the DT needs to deliver far more value to continue to serve this community.
As a result of these expectations, most conversations around DT in industry involve serious thoughts around solutions that have one or more of the following domains:
- Asset or product design activity, i.e., engineering
- Asset or product manufacturing process activities, i.e., operations
- Value creation from product or asset feature engineering, i.e., services
This requires solution providers to address functions from both the digital and physical worlds that define the asset. While the physical world comprises:
- Actual asset
- Level (Level 0, Level 1, Level 2, etc.) of control automation pyramid
The digital world defines virtual mapping of the asset as per its properties:
- Business
- Function
- Communication
- Integration
- Type
- Instance

This is where the Reference Architecture Model for Industry 4.0 (RAMI 4.0) plays a foundational role, as a service-oriented architecture, to combine all elements and IT components in a layer and lifecycle model, thereby rendering the Purdue model all but obsolete [3].
In the ‘object’ world of Industry 4.0 (I4.0), RAMI 4.0, with its 3D coordinate axes of hierarchy levels, lifecycle value stream and layers, helps break down complex processes into smaller and manageable sections of an asset. As per the International Electrotechnical Commission (IEC) 63088, it also ‘describes assets with sufficient precision.’ [5]
By defining the asset in such detail, solution providers now have a complete visibility for designing a DT that cuts across the physical and digital existence of the asset.
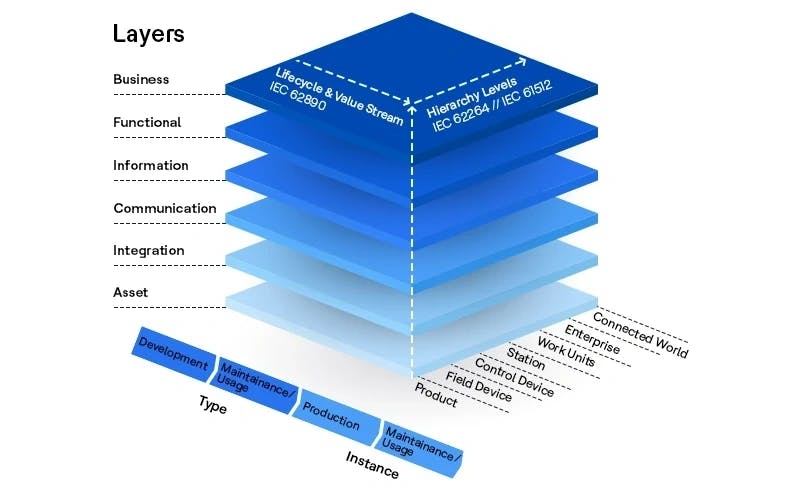
In the next blog post, we explain how with this foundation in place, it is possible to not only have smart products with a twin ‘at birth’ as a result of their inherent design but also have ‘clones’ known as components, assets, systems and process twins, long after their original construction, by leveraging the Asset Administration Shell.
References:
- “How Smart, Connected Products Are Transforming Competition,” M.Porter and J.Heppelmann, HBR
- “Robust Digital Twin,” Dan Miklovic
- “A reimagined Purdue model,” Forbes
- LNS Research (lnsresearch.com)
- International Society of Automation (isa.org)