In today's fast-paced world, it has become an imperative for any energy solution provider to ensure seamless and uninterrupted power generation and supply. Our customer, a leading sustainable energy solutions provider in Europe, faced difficulty ensuring continuous, uninterrupted operation of their wind turbines installed across the globe. They sought a remote maintenance solution that would facilitate monitoring the performance of their wind turbines, predict future breakdowns and perform root cause analysis on persistent failures of their subsystems. After partnering with HCLTech to accelerate progress, we developed a game-changing Product Twin platform to assist them in achieving these objectives from anywhere in the world.
The Challenge
Overcoming high failure rate of wind turbine drive trains
Our customer is a global leader in sustainable energy solutions, providing design, manufacture, installation and maintenance services to wind energy and hybrid projects worldwide. They were experiencing high failure rate of their wind turbine drivetrains on field, leading to increased downtime, maintenance and warranty costs for the turbine fleet. They were facing various challenges in identifying the root cause of these frequent failures, which was impacting the wind turbine performance, availability and safety, consequently resulting in revenue loss.
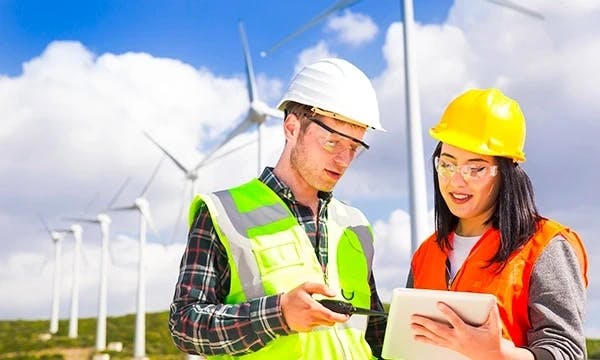
The Objective
Remote monitoring and root cause analysis solution to reduce asset downtime and save operational cost
The client sought a reliable remote maintenance solution that could leverage on-field operating data to:
- Proactively analyze the performance of the turbines
- Predict equipment downtime upfront
- Identify the root cause of drivetrain failures
They intended to utilize the insights provided by our solution to optimize their product design and development process, creating better products in the future and increasing the ROI.
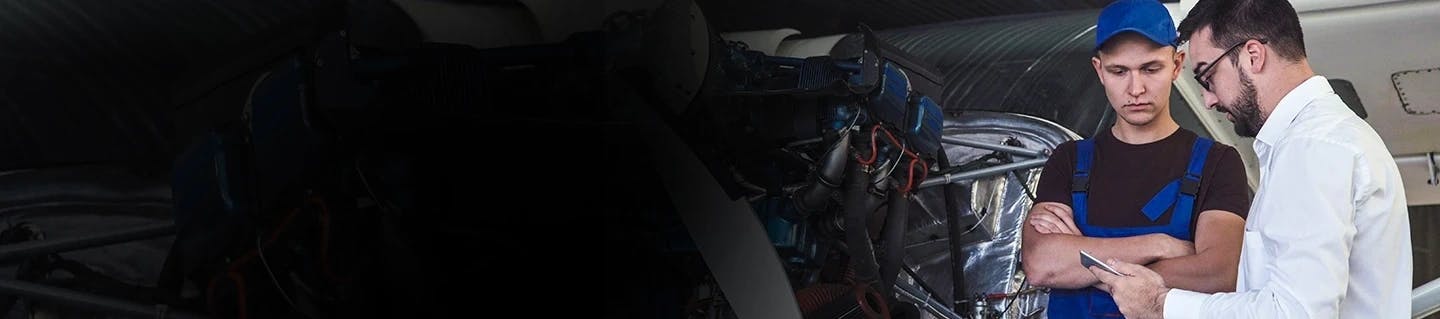
The Solution
A game-changing Product Twin platform for remote monitoring and analysis of wind turbines
We developed a Product Digital Twin platform using an advanced technology stack to remotely monitor, simulate and predict performance of wind turbines. Our solution facilitated the adoption of a closed-loop Digital Twin solution to combine end-to-end horizontal engineering, design, manufacturing and operational processes. It assisted in aggregating and normalizing the operational data gathered by IoT sensors to produce a virtual replica of the physical assets (wind turbine drivetrains). Additionally, it combined operational data with field conditions and superimposed the output on virtual simulation models to recreate field behavior and helped in identifying the root causes of equipment failures and validating them against product specifications, resulting in improved efficiency, less downtime and increased productivity.
The Impact
Minimal downtime, maximized product performance and improved next generation of products
By leveraging our Product Twin platform, the client was able identify risks during design, manufacturing and commissioning, leading to improved next generation products and significantly reducing failures.
Our platform empowered the client to achieve remarkable outcomes, including:
- Upto 20% reduction in downtime due to lower MTTR (Mean Time to Repair)
- Upto 15% optimization in product performance
- Upto 30% reduced warranty and maintenance costs