The Challenge
The client, a prominent manufacturing company, sought to optimize its complex manufacturing value chain across 20 key sites. Their challenge was magnified by a stringent high-speed manufacturing process where even a few minutes of delay between operations would result in significant production loss, and they needed to achieve this optimization without significant capital investment.
To further its overall business transformation goals—encompassing enhanced manufacturing quality and productivity, reduced production costs, improved employee productivity and safety and accelerated time to market—the company aimed to establish a more agile and responsive approach to demand fluctuations.
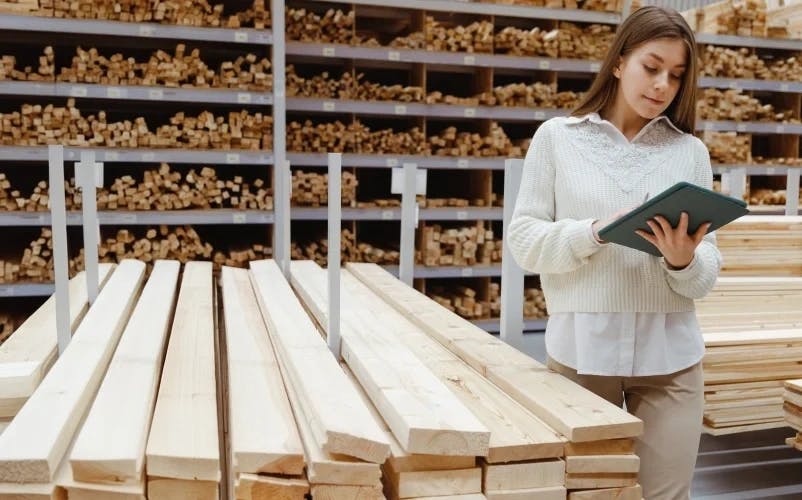
The Objective
Value chain optimization
- Achieve streamlined and efficient operations across the entire manufacturing value chain, encompassing 20 sites and 3 critical operation assets
Process robustness
- Enhance the manufacturing process to minimize downtime and ensure seamless transitions between operations, even within tight tolerances
Production efficiency
- Increase production run rate and ensure the manufacturing process operates at peak efficiency
Uptime maximization
- Reduce unplanned downtimes and boost overall production uptime from 70% to 80%
AI-powered productivity
- Leverage Industrial AI to gain real-time visibility into productivity KPIs (like OEE, uptime, speed, average gap and more), identify performance deviations for proactive intervention and enable operator guidance with 30-minute advance asset failure warning.

The Solution
HCLTech addressed the manufacturing optimization challenge by deploying its AI-led advanced analytics solution, Real-time Manufacturing Insights (RMI). Leveraging the capabilities of AI, Edge AI and Gen AI, RMI facilitated actionable intelligence delivery directly to the production floor, thereby transforming the manufacturing landscape across the client's extensive network.
Data-driven insights
- RMI's AI engine conducted a comprehensive analysis of manufacturing data, identifying over 100 causal parameters that contributed to critical production KPIs. Further analysis successfully isolates 10 critical factors responsible for 80% of downtime. Employing its inbuilt ML builder, RMI generated and deployed algorithms tailored to these specific scenarios, furnishing near-real-time insights to operators within an impressive reduction from 5 minutes to 30 seconds.
Proactive intervention through Gen AI
- Gen AI augmented these insights by integrating them with historical data on failures and corrective actions. This integration enabled Gen AI to provide line operators with clear, concise instructions for proactive intervention, empowering them to pre-empt asset failures and effectively contribute to minimizing downtime.
Measurable business impact
- The deployment of RMI yielded a substantial impact, extending across the client's 20 sites. Through predictive maintenance and operational optimization, RMI translated operational data into tangible financial gains, delivering a bottom-line impact of $600 million.
- HCLTech RMI is an AI-powered digital twin solution that provides a holistic view of manufacturing operations. By leveraging IoT and AI/ML models, RMI delivers role-based insights and real-time intelligence, enabling proactive decision-making. Edge-AI and Gen AI further transform shop floor data into actionable insights, optimizing asset efficiency and productivity
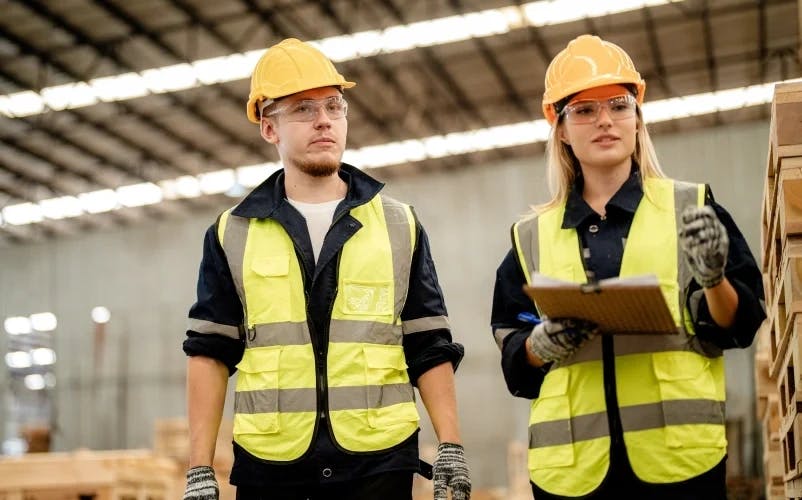
The Impact
- Increased production uptime from 70% to 80%
- 30-minute advance asset failure warning
- Reduced unplanned downtime for operations and cost savings of ~30%
- Improved mill productivity by 10%
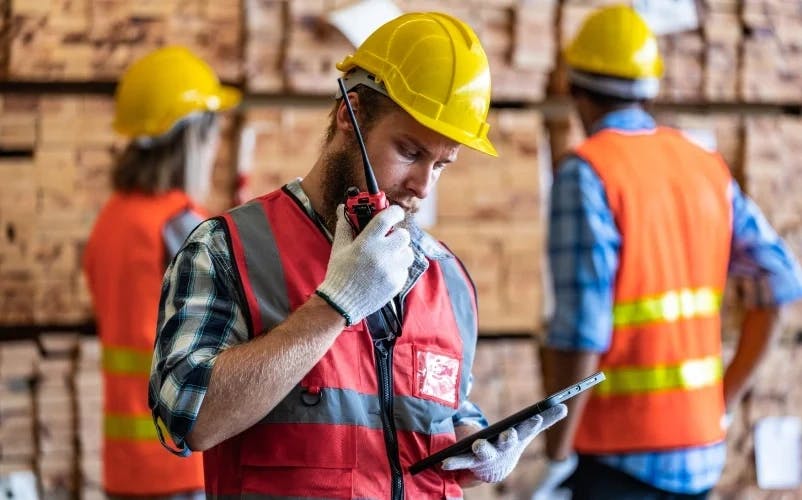