Our client is a leading independent provider of assembly and test services for a broad range of semiconductor chips, including in-communication, consumer, computing, automotive, security devices and industrial and medical applications. They have a manufacturing footprint of over 260,000 square meters in Singapore, Thailand, Indonesia and China.
The Challenge
Inefficient supply chain processes
Our client faced challenges in processing massive amounts of data from the source system. Key challenges included:
- Inefficient inventory management
- Inefficient integration solution to process the data from the source system
- Complex supply chain landscape with different sources of data (inbound and outbound)
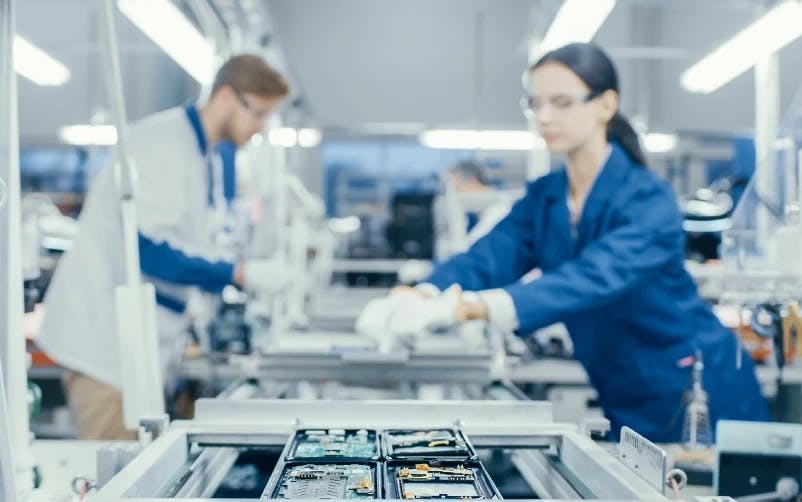
The Objective
Improve the supply chain system
Our client was looking for a partner with a good mix of technical and supply chain expertise to understand their system and provide the right solution for their business growth. Their key objectives included:
- Compatible source system with Blue Yonder Enterprise Supply Planning (ESP) System
- An integration solution to process massive data from the source system, such as SAP, Oracle DB, Anaplan and other Excel files
- Simplified application landscape for supply chain planning
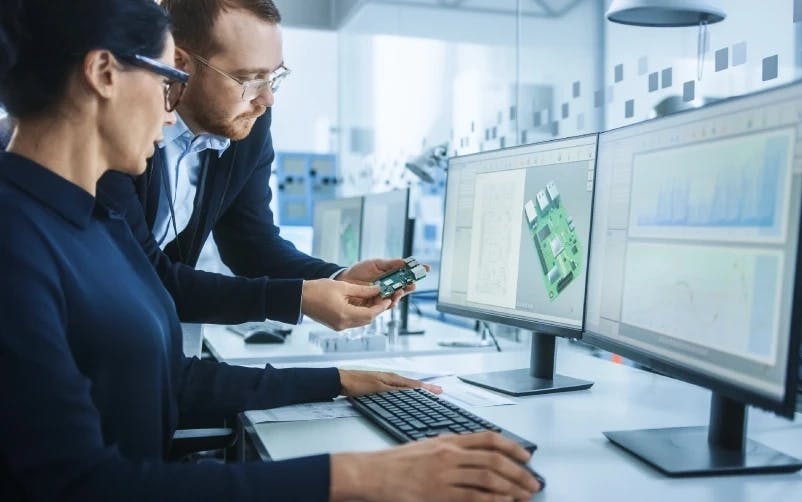
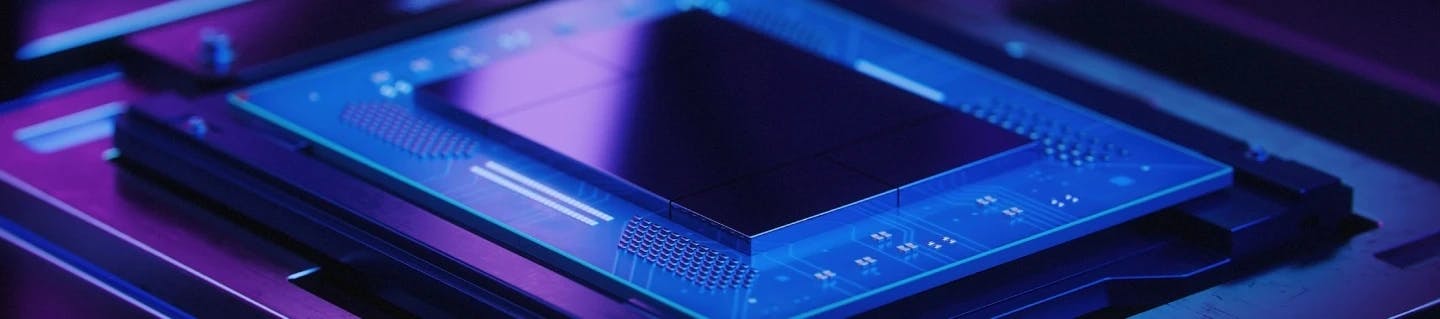
The Solution
Efficient supply planning solution
HCLTech conducted an extensive exercise to arrive at the right solution, beginning with 8 weeks of cross-functional discovery workshops with the client. Our key solution included:
- Implementation of demand classification, safety stock calculation, moving event and supersession solutions
- Transformation from Push model to Pull model (based on Store demand) to respond immediately against demand spikes and cater to rapid adaption for changing customer preferences
- Development of a list of APIs to pull the data from different client group source systems and generation of CSV files
- Development of 64 complex Reports in the Power BI platform
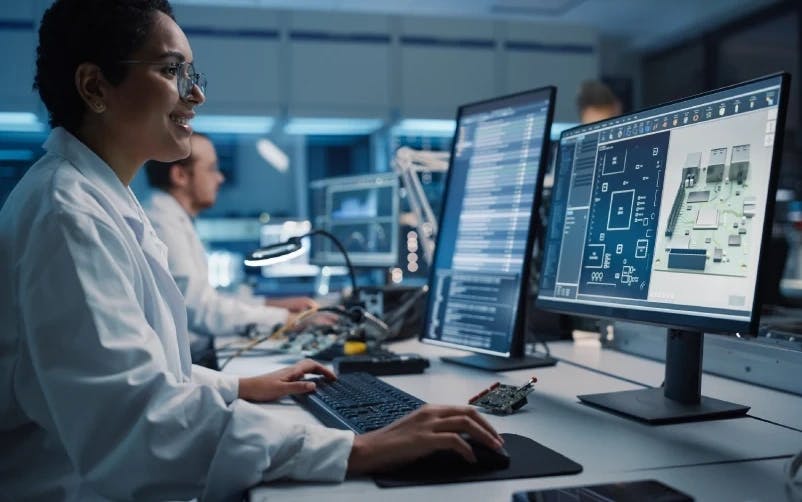
The Impact
Optimized processes and improved productivity
Our client reaped the following benefits from our solution:
- 8% reduction of inventory at the store and 25-30% at the warehouse
- Improved supply chain visibility, leading to optimized order quantities and a reduction in safety stock level by 10-12%
- 20% improvement in productivity of supply chain processes
- 30% reduction in distribution expenses
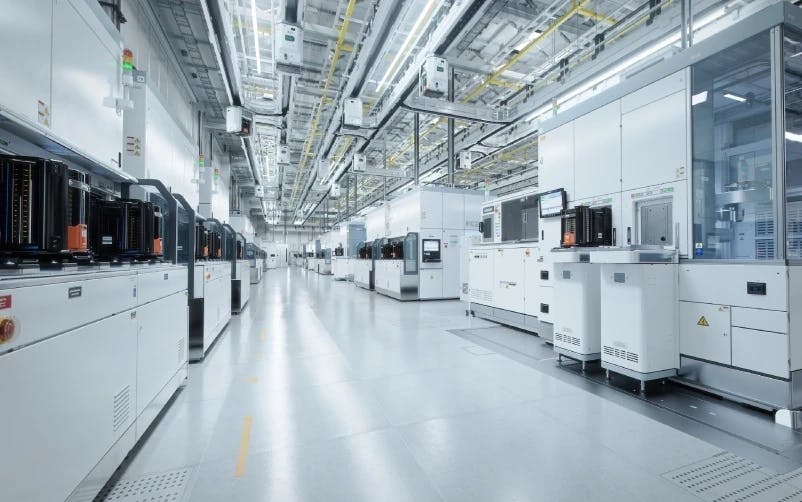