Our client is the world's largest tool manufacturing company, renowned for its engineered fastening systems. With a workforce of over 60,000 individuals and a presence in 60+ nations, the company generates substantial revenue in tools and outdoor equipment, alongside highly engineered industrial products.
The Challenge
Overcoming manual challenges for operational efficiency
Our client sought to modernize packing processes through the implementation of cutting-edge automation technology. Prior to automation, they faced several challenges:
- Manual packing processes: The packing process relied heavily on manual intervention, with orders being manually deposited and searched for in the packing machine, leading to operational inefficiencies
- Disciplinary challenges: Personnel compliance with manual scanning procedures posed disciplinary challenges, resulting in orders sometimes being overlooked or not processed efficiently
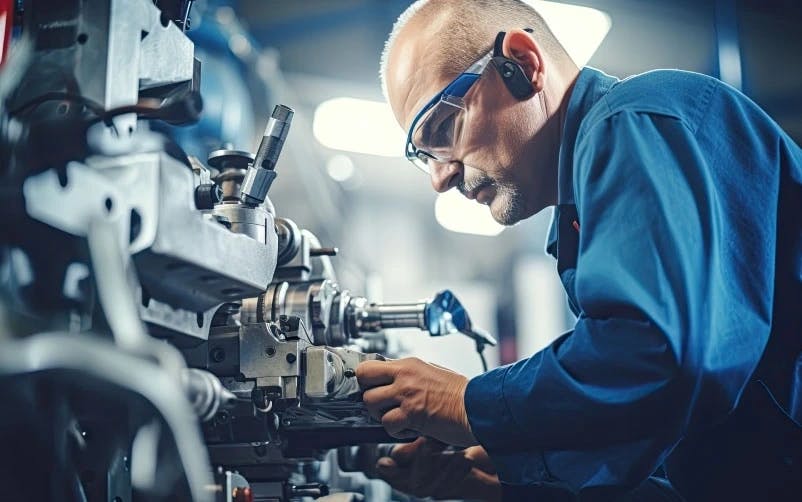
The Objective
Pursuing operational excellence
Our client aimed to revolutionize packing processes by implementing automation technology, driven by objectives to enhance production speed, improve information access and optimize overall operations. By automating infeed and outfeed to packing machines, they sought to streamline operations, reduce manual errors and accelerate turnaround times. Integration with existing systems aimed to provide real-time visibility into order status and inventory levels, empowering informed decision-making. Ultimately, the goal was to achieve operational excellence, minimize wastage and enhance customer satisfaction, positioning our client as a leader in the competitive manufacturing industry.
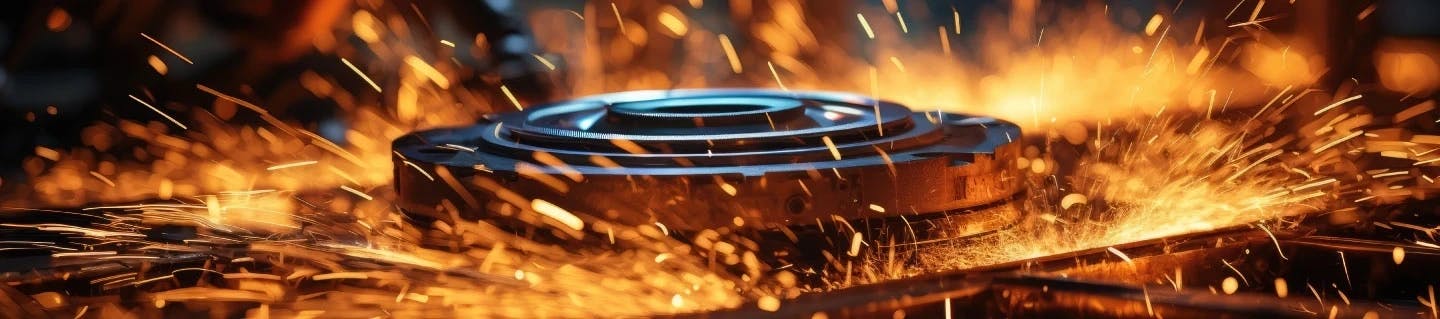
The Solution
A comprehensive solution for streamlining operations
To address the challenges and meet the objectives, we implemented a comprehensive solution:
- Automated packing machine installation: As part of an Industry 4.0 initiative, we installed a highly automated small part packaging machine from Bonotto. This machine facilitated the automated packaging of small parts, streamlining the packing process.
- Integration with Blue Yonder WMS: Leveraging our client's existing Blue Yonder Warehouse Management System (WMS), we developed an interface to transmit order line information directly to the installed packaging machine. This integration enabled end-users to prioritize and optimize orders for packaging.
- Enhanced information access: The solution generated pull lists for bulk products and provided the vendor with label formats and variable data to generate box and sleeve labels, improving access to critical information throughout the packing process.
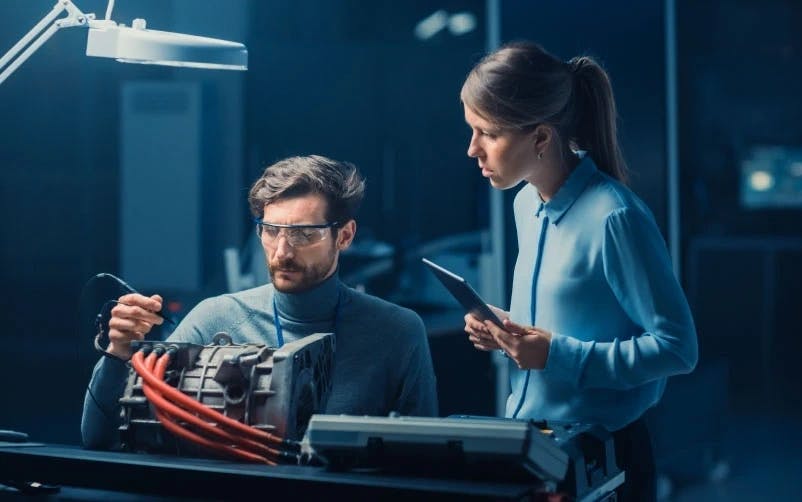
The Impact
Production speed and cost efficiency
The implementation of the automated packing solution yielded significant benefits:
- Automated packaging of small parts enhanced production speed, translating into enhanced business cost efficiency and operational effectiveness
- The automation of packing processes led to improved quality control, ensuring consistency and accuracy in packaging operations
- The solution facilitated better access to critical information throughout the packing process, enabling smoother operations and informed decision-making
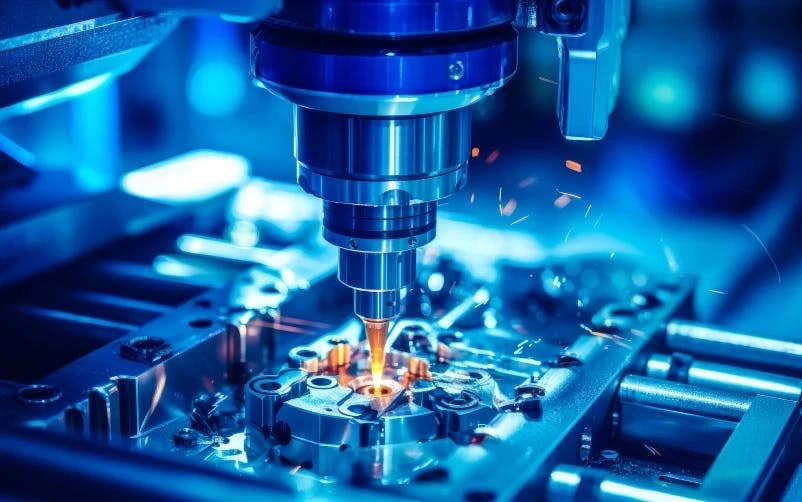
The adoption of automated packing processes not only improved production speed and cost efficiency but also enhanced quality control and information access, positioning our client for greater operational excellence in their manufacturing operations.