About the Client
Our client, a leading equipment supplier driving cutting-edge technology and solutions for inspection and metrology, entrusted HCLTech to sustain their legacy product in accelerating next-gen electronic devices.
The Challenge
Enhancing legacy product support and innovation strategy
The world's leading metrology and inspection equipment manufacturer sought robust support for their legacy product as it was straining resource availability for new product R&D. The client was also looking to navigate the industry's ever-evolving landscape and stay ahead of technological advancements. The key challenges included:
- Servicing escalations originating from a large installed base in fabs spread across the world
- Developing new and customized features to meet the specific client needs of end customers
- Addressing communication and collaboration issues between engineering groups within the organization working in silos, which caused delays
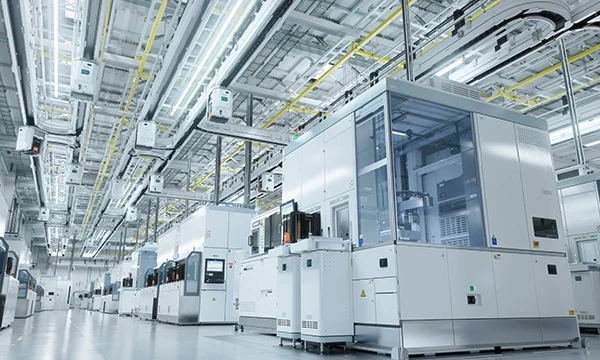
The Objective
Revolutionizing semiconductor equipment support and innovation
We, at HCLTech, devised a strategic plan to address our client's unique requirements and pain points. With an objective to extend the lifespan of semiconductor equipment through our offerings, we focused on minimizing the time-to-market of new products and unlocking unparalleled efficiency, precision and scalability levels. The primary objectives of our plan included:
- Enhancing equipment reliability through adequate maintenance and monitoring
- Extending the life of legacy equipment through smart upgrades and effective management
- Developing a knowledge management system to effectively improve quality and productivity as well as measure deliverables through processes showcasing continuous improvement
- Automating test cases and integrating with continuous improvement to reduce the cycle time
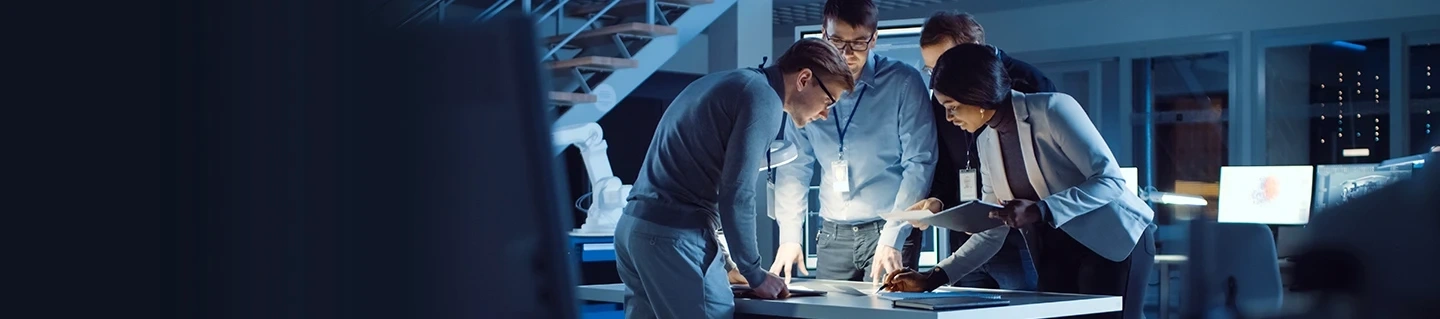
Our Approach and Solution
Delivering cutting-edge engineering solution through comprehensive analysis and innovative approaches
Our expertise gained over two decades of our transformational presence in the industry has rightly positioned us to address the unique requirements of the industry and clients. Facilitated by our best-in-industry labs and testing infrastructure, solutions, accelerators and frameworks, we are able to meet our clients' demands.
To craft a personalized solution for our client, our team conducted a comprehensive analysis of their pain points and specific needs to create a personalized solution that aimed to extend the lifespan of their legacy products. Our dedicated wafer loader lab facilities and an integrated engineering solutions approach spanning software, electrical, hardware and testing services delivered superior results to the client, making us their most preferred, reliable and trusted partner. The following results were achieved:
- Automated over 3000 test cases and increasing test coverage by 80%
- Provided bug fix and escalation support, developed more than ten new features and conducted training events
- Supported complete firmware layer for machine interface boards redesigning hardware boards
- Redesigned over 150 electrical cables and electromechanical components
- Effectively managed obsolescence needs and reconfiguration requests.
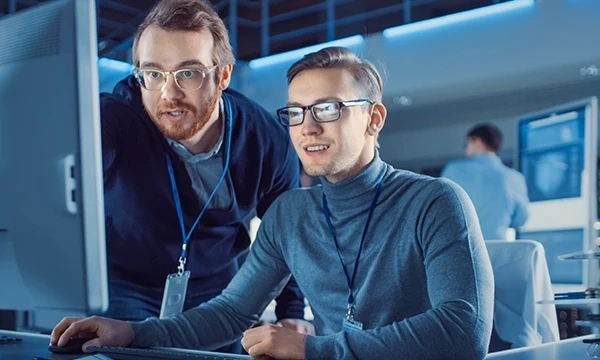
The Impact
Driving innovation and value through collaborative solutions
Our expertise and solutions played a crucial role in helping our client overcome challenges and unlock their true potential. Through our innovative collaboration, we achieved remarkable outcomes, enabling them to achieve a reduction in product-related issues reported by end customers and faster time-to-market. Some key highlights include:
- We helped our client expand into four product areas: critical dimension, thin film, overlay and resistive measurement.
- Escalation SLA was reduced from three days to four hours.
- Manual testing effort was drastically reduced from 100 hours to eight hours.
- We supported more than 25 fab visits, providing engineering support across geographies and time zones, seamlessly collaborating with the client’s global team and end customers' installed base across Europe, Southeast Asia and North America.
- We developed a large 3000 sq ft lab to support the client, which acts as a collaboration zone for engineering development and training new customer field technicians and R&D engineers.
- We developed more than 500 new software features for end customer requirements.
- Our services span across all engineering divisions, global services and IT operations of the client, optimizing operations through effective collaboration.
- Last but not least, our global development centers provided significant cost advantages.
We are committed to continuing our collaborative efforts, driving innovation and delivering exceptional value to the client as their trusted partner.